PLC and Edge Computing: Driving Real-Time Control in Industrial Automation
PLC and Edge Computing: Driving Real-Time Control in Industrial Automation
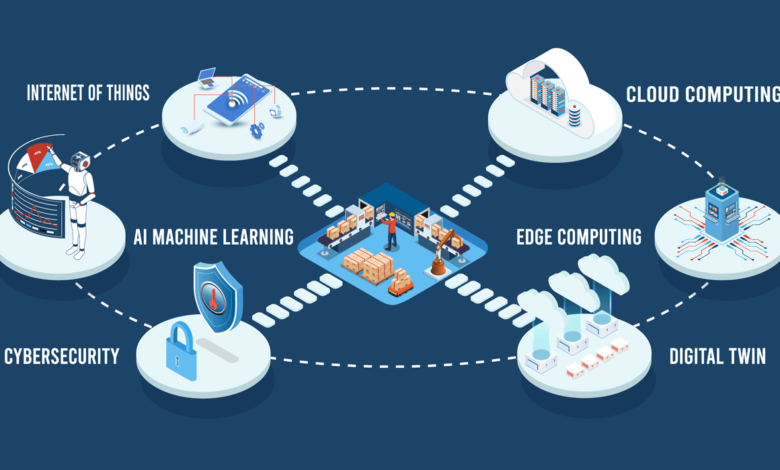
In the rapidly advancing world of industrial automation, two technologies stand out for their role in optimizing control systems and enhancing operational efficiency: Programmable Logic Controllers (PLCs) and Edge Computing. Let’s explore how these technologies are revolutionizing how data is processed and controlled within industries.
Download PDF: PLC Interviews Questions with Answers
Understanding PLCs in Industrial Automation
A Programmable Logic Controller (PLC) is a robust, industrial-grade computer that controls manufacturing processes and automation systems. Unlike traditional computers, PLCs are built to withstand harsh environments and offer high reliability, ease of programming, and scalability for complex industrial tasks.
PLCs receive inputs (e.g., sensors, switches) and execute pre-programmed logic to produce outputs (e.g., controlling motors, pumps, or actuators). They are essential in automating repetitive tasks, ensuring precision, and improving system uptime.
Download PDF: PLC PROGRAMMING
The Role of Edge Computing
Edge Computing refers to processing data near the source of data generation rather than relying solely on a central server or cloud infrastructure. By analyzing and processing data locally on the “edge” of the network (i.e., closer to the devices), edge computing reduces latency and the need for constant communication with distant servers.
Edge computing is particularly valuable in industrial automation because it enables real-time data processing and decision-making. This leads to faster response times, improved system reliability, and reduced dependency on internet connectivity.
Download PDF: OIL AND GAS PLC FUNDAMENTALS TRAINING PDF
How PLCs and Edge Computing Work Together
When integrated, PLCs and Edge Computing create a powerful solution for industrial automation. Here’s how they complement each other:
- Localized Data Processing: With edge computing, data can be processed on-site, closer to where the PLC operates. This allows for faster decision-making and response times, reducing delays often seen in cloud-based solutions.
- Improved System Efficiency: By reducing the amount of data sent to the cloud or a central server, edge computing minimizes network congestion, ensuring that the PLC can execute tasks without interruption.
- Predictive Maintenance: With edge computing, PLCs can analyze data from sensors in real-time, enabling predictive maintenance. This helps industries to foresee equipment failures before they occur, reducing downtime and maintenance costs.
- Increased Scalability: As industrial systems grow, the integration of PLCs and edge computing makes it easier to scale operations without overwhelming the network, ensuring smooth and continuous control.
Download PDF: PLC Programming for Industrial Automation
The Benefits of Industrial Automation
- Enhanced Performance: By processing data at the edge, the systems become more responsive, leading to optimized control of industrial processes.
- Reduced Latency: Localized processing enables instantaneous decision-making, critical in high-speed automation tasks.
- Cost Efficiency: With less reliance on centralized cloud servers, businesses can reduce data transmission costs and manage resources more effectively.
- Improved Security: Edge computing reduces exposure to cyber risks by limiting the need to send sensitive data across the network,
Conclusion
As industries continue to adopt more complex automation systems, the synergy between PLCs and Edge Computing becomes crucial. Together, they enable localized data processing and control, fostering more efficient, responsive, and secure industrial environments.
Stay tuned for more insights on Electrical Fundamentals and how emerging technologies continue to shape the future of electrical engineering!